Началом истории комбината принято считать 1910 год, когда в Чите появились лесопильные цеха, которые затем стали заниматься более глубокой переработкой древесины. Во время Великой Отечественной продукция лесопильного завода шла на фронт. В спокойные 60-е здесь выпускали писк тогдашней моды - полированную мебель. В 2000 году предприятие получило современное название - Читинский мебельный деревообрабатывающий комбинат «Даурия». Спустя несколько лет слово «Даурия» исчезло. Сейчас комбинат занимается только изготовлением мебели - корпусной, мягкой и офисной - как по типовым проектам, так и по заказам. Объём продукции, выпускаемой за месяц, составляет от 3 до 4,5 миллиона рублей.
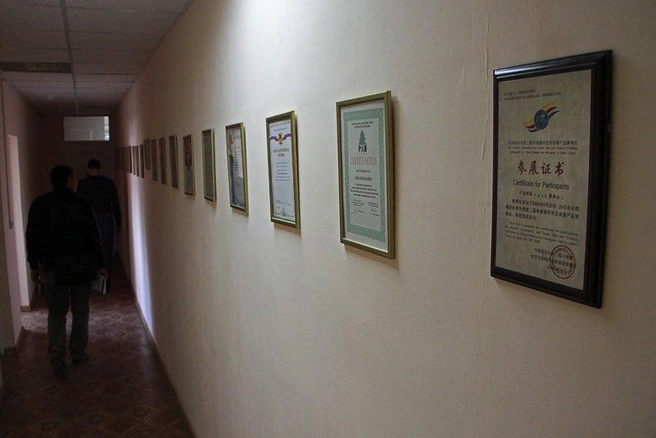
Процесс изготовления корпусной мебели начинается с распилки ламинированных древесно-стружечных плит (ЛДСП). Работают на этом станке два человека. Один выставляет размеры будущих стенок и дверец, направляет листы на режущий диск. Второй принимает и ловко сортирует заготовки.
Опилок и пыли около пилы, как и в целом по цеху, почти нет. Все станки оборудованы вытяжной внутренней вентиляцией. Попадая в неё, тяжёлые частицы оседают в больших мешках, а лёгкие - на стенках фильтров.
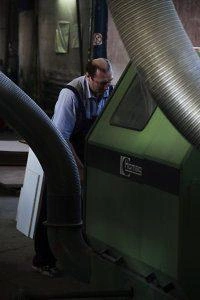
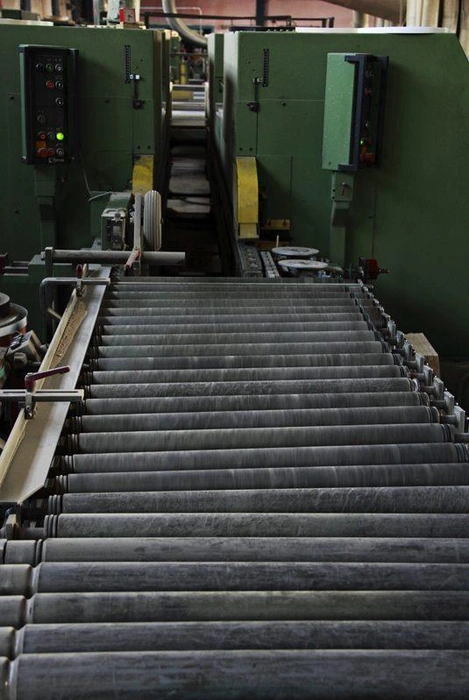
Распиленные заготовки увозят на длинную автоматизированную линию, которая обрабатывает их по размеру и наклеивает на место спила кромочную ленту. Этот станок рассчитан на обработку большого количества деталей. Заготовки нестандартной формы обрабатываются на другом станке.
«Для обработки нескольких заготовок данная линия малоэффективна. Настройка занимает около 10 минут, а на работу уходит гораздо меньше. Однако за последнее время часто выполняются индивидуальные заказы, и нам приходится это делать», - поясняет начальник отдела сбыта Андрей Рюмкин.
Заготовки с обработанными кромками попадают на присадку - то есть сверление отверстий для креплений и фурнитуры. Этим занимается Анастасия, которая трудится на комбинате более 10 лет. Опыт видно сразу - точными движениями она ловко управляется и с техникой и с ДСП. Работа здесь довольно монотонная, поэтому женщина обслуживает два станка одновременно - для разнообразия.
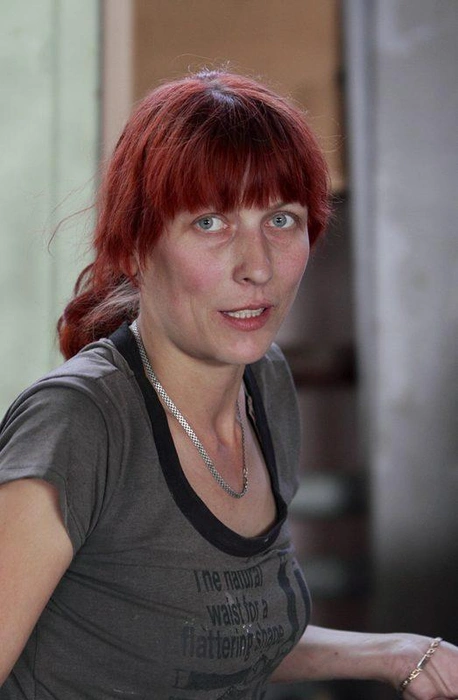
«Пять минут и сделали низ для двух кухонь», - говорит Анастасия.
Если заготовка предназначена для фасада, то её отправляют на обрабатывающий центр с числовым программным управлением. Он вырезает в плите МДФ (англ. Medium Density Fiberboard - древесно-волокнистая плита средней плотности) отверстие для стекла или декоративное углубление. Смотреть на такую работу — одно удовольствие. Рабочий вводит необходимые параметры, а бегающая головка станка делает своё дело.
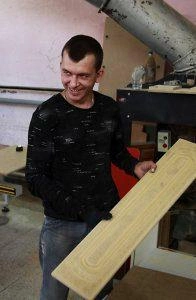
В следующем цехе на детали наносят плёнку или краску. Покраска — это вполне обычный процесс. В камере с деталей удаляют загрязнения, включают водяную завесу для защиты от пыли и распылителем наносят краску или лаки. После просушки в другой камере части отправляют на сборку.
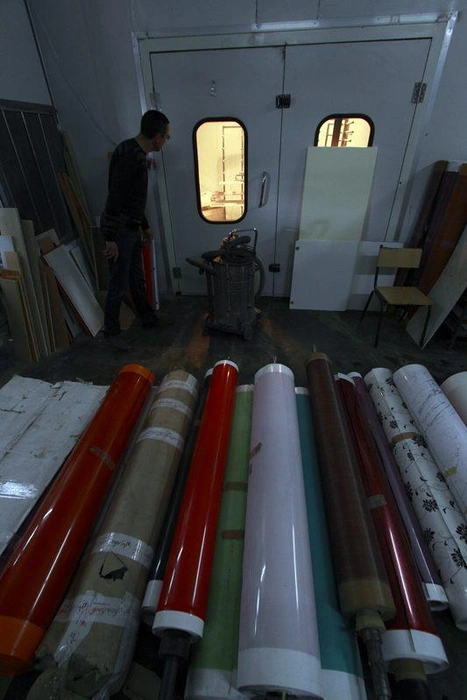
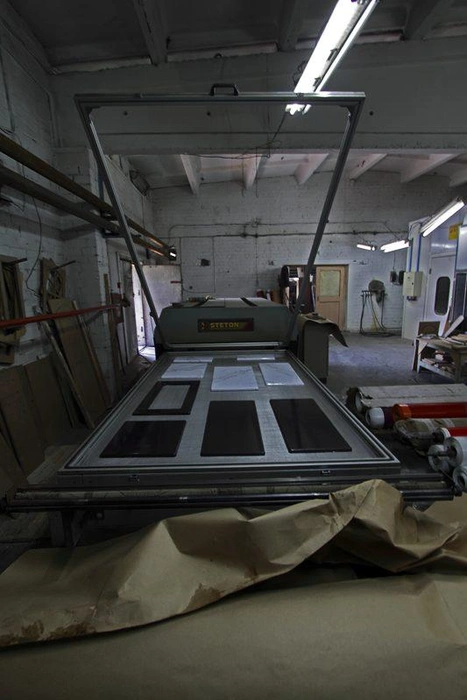
Покрытие плёнкой - более сложный процесс, выполняемый на специальном вакуумном прессе. В первую очередь заготовки покрывают особым клеем. Затем раскладывают на прессе и накрывают плёнкой, которая натянута на рамку. Сверху задвигается нагревательный элемент станка с трубчатыми электронагревателями (ТЭНами). Когда нагревательный элемент находится в рабочем положении, внутри повышается температура, и создаётся вакуум. При температуре около 70 градусов происходит активация клея, а вакуум заставляет плёнку ровно и плотно повторить формы заготовки. Через некоторое время готовые детали также идут на сборку изделия.
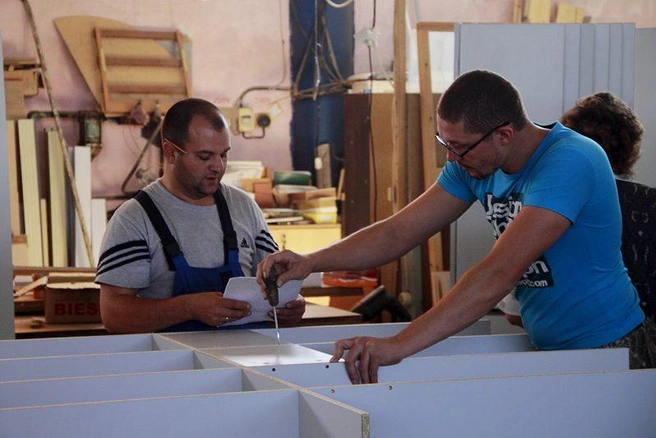
На комбинате есть возможность печати любого изображения на МДФ, стекле или зеркале. Рисунок можно выбрать в каталоге или принести с собой. Важное звено цеха - участок контроля, на котором все детали проходят проверку. Всё, что имеет царапины, сколы и неровности, отправляется в брак.
«Раньше мы изготавливали много типовой мебели, а сейчас работаем по спецзаказам. Хотя оборудование предназначено именно для больших партий одинаковых деталей. Чтобы загрузить станки мы участвуем в тендерах. Сейчас, например, изготавливаем оборудование для районных судов - скамьи, трибуны, подставки для флагов. Спецзаказ - это не всегда что-то необычное. Чаще всего заказчикам нужно подогнать мебель по размерам. Хотя интересные заказы тоже бывают. Например, красивые ажурные стенки. Стойка в баре кинотеатра «Удокан» - тоже наша работа, и, как мне кажется, получилось вполне достойно», - рассказал Андрей Рюмкин.
В цехе мягкой мебели всё совершенно иначе. Здесь меньше шума, но больше ярких цветов. Производство начинается на первом этаже - там также строгают и пилят доски, из которых собираются каркасы будущих диванов и кресел. Затем конструкции поднимают лифтом на второй этаж.
Первая операция - это обивка поролоном. Его достают из стопки, на которой немедленно хочется попрыгать, и нарезают электроножом. Облачённые в поролон конструкции мало похожи на мебель. Но красоту будут наводить позже - для этого потребуется труд ещё нескольких человек. В первую очередь закройщиков.
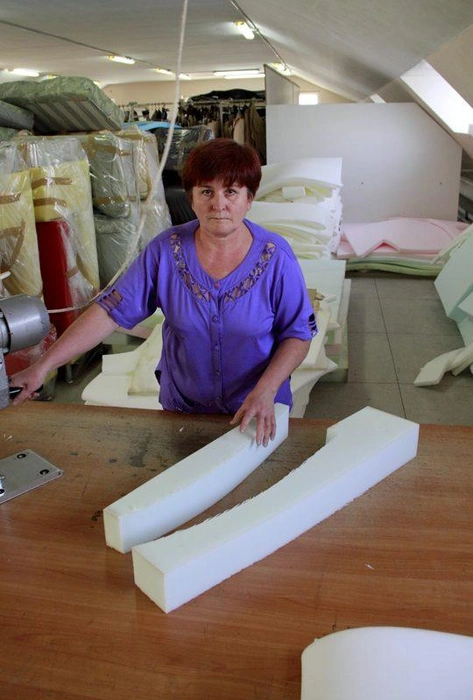
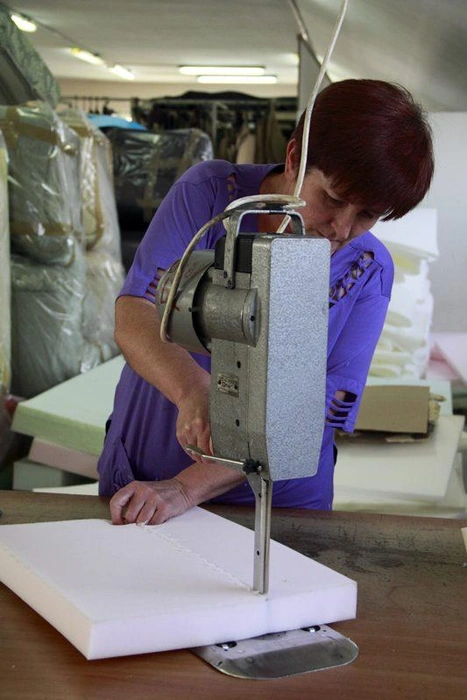
На их рабочем месте - огромном столе - расстилается без морщинок и складок обивочная материя. Затем её расчерчивают мелом и кромсают электроножом. Выкройки идут к швеям.
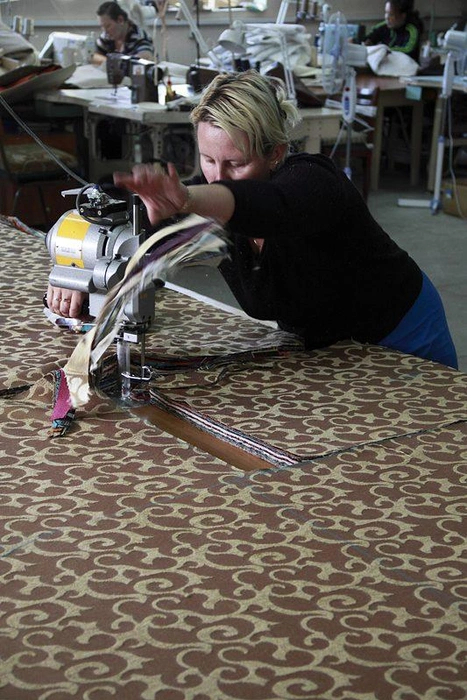
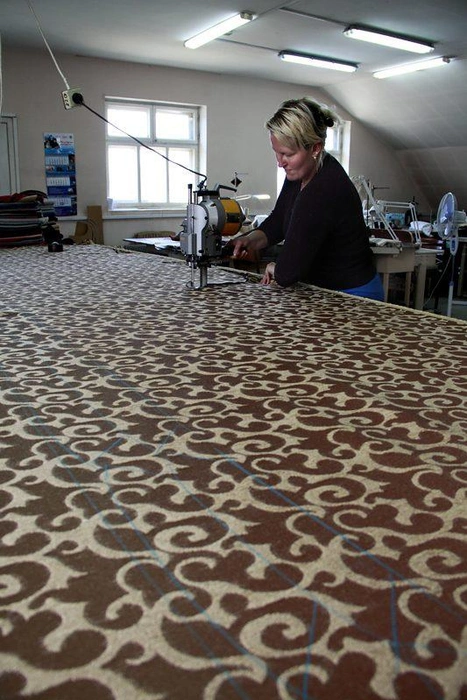
Их работу здесь называют сложной. Кожа и другие обивочные материалы - это не ткань для платьев - для её прошивки требуются мастерство и усилия.
Готовую одёжку на мебель надевают раз и навсегда с помощью пневмостеплеров. Крепкие мужчины крутят спинки, подлокотники и сиденья, облекая их тканью.
«На рынке мягкой мебели у нас больше конкурентов. Если качество корпусной и офисной можно оценить сразу, то внутрь дивана или кресла никто не заглядывает. А добротность материалов можно оценить только через какое-то время», - рассказал Андрей Рюмкин.