Читинский силикатный завод начал работать в Чите в 1963-м, выпустив до конца года 30 миллионов штук кирпича. К середине 80-х производство выросло до 200 миллионов штук. В советское время завод обеспечивал стройматериалами не только Забайкалье и соседние регионы, но и Монголию. К началу нового тысячелетия завод освоил производство железобетонных изделий, тротуарной плитки, но главной продукцией по прежнему остаётся кирпич.
Летом, в жаркий строительный сезон, завод выпускает до 500 пакетов кирпича, в каждом из которых 660 штук. Сейчас, когда строители уже заканчивают объекты, производство снижается до 100-200 пакетов. После Нового года предприятие забивает готовыми кирпичами все площадки и останавливает производство примерно на три месяца.
Обыкновенный силикатный кирпич состоит из трёх главных компонентов — извести, которая выполняет роль вяжущего компонента, песка и воды. Для получения цветных в смесь добавляют краситель.
Известь на силикатном заводе — привозная. Её доставляют вагонами с Урала и разгружают на известковом складе. Песок добывается на карьерах в Атамановке и Антипихе.
Со склада известь поступает на мельницу, где её измельчают до порошкообразного состояния. В помещении, как на настоящей мельнице, всё белым-бело.
В это время песок из бункеров проходит через сито-бурат и очищается от камней и корней. Затем их доставляют в массоприготовительное отделение — на пятый этаж. Песок едет туда на транспортёре, а известь поднимается мощным пневмонасосом.
На четвёртом этаже находятся дозаторы, которые составляют массу из определённых пропорций компонентов. Затем масса спускается на третий этаж — в мешалку, а потом ниже — в большие ёмкости, которые называются силосами. Там происходит гашение смеси — идёт она 2-3 часа в зависимости от активности извести.
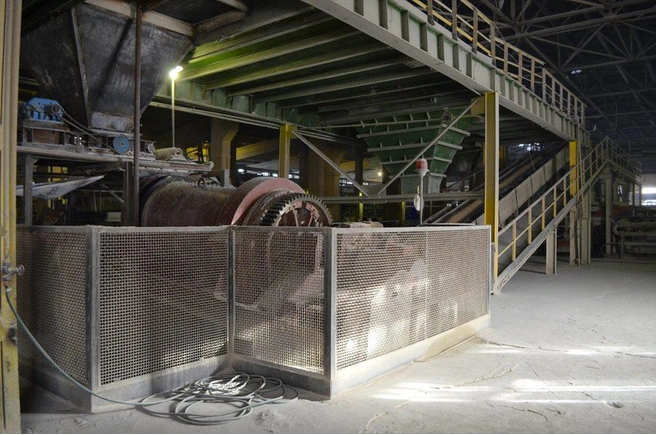
Из силосов готовая масса забирается питателями и забрасывается на вторичное перемешивание в лопастных мешалках. Ещё одно перемешивание и дополнительное измельчение будущие кирпичи проходят в стержневом истирателе. До него масса тоже доезжает по ленточному конвейеру, общая длина которого на заводе — около километра.
По одной линии масса поступает на два гидравлических пресса, которые формируют массу в ровнейшие прямоугольники. Пресс №1 работает с 2003 года и за один ход поршня делает пять кирпичей. Второй — более современный и производительный. За раз он изготавливает семь кирпичей.
На другой линии работают настоящие ударники производства - одинаковые немецкие прессы №3 и №4. Оба за одно движение штампуют по 14 кирпичей. Задача пресса состоит не только в том, чтобы придать массе форму, но и в том, чтобы сжать её максимально сильно, не оставляя свободного пространства.
Пресс самостоятельно берёт свежеприготовленную партию и кладёт её на вагонетки. У меня этот кирпич-сырец вызвал ассоциацию с новорождённым ребёнком — такой же мокрый, тёплый и нежный. Сделать царапину на боку силикатного младенца легко даже ногтем.
Требуемую крепость сырцам придают в автоклаве. За раз в одну помещают 14 вагонеток, постепенно повышают температуру до 180 градусов, а давление до 8-10 атмосфер. В автоклаве кирпичи томятся 12 часов. Первые два часа давление поднимается, а два последних — сбрасывается.
Также на заводе работает производство тротуарной плитки. Процесс здесь, в целом, похож на производство кирпича, но менее автоматизирован.
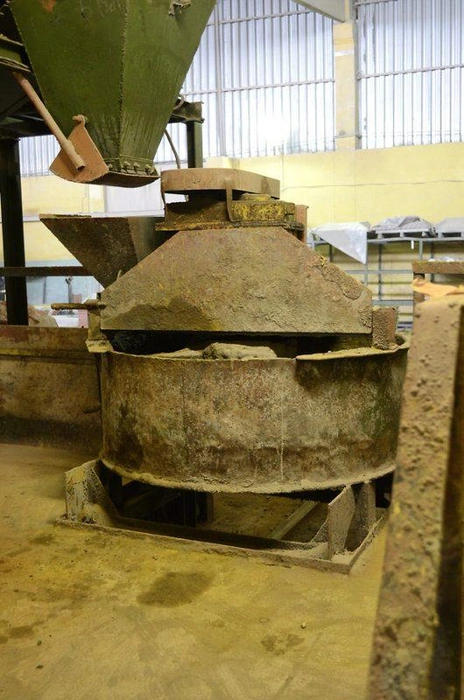
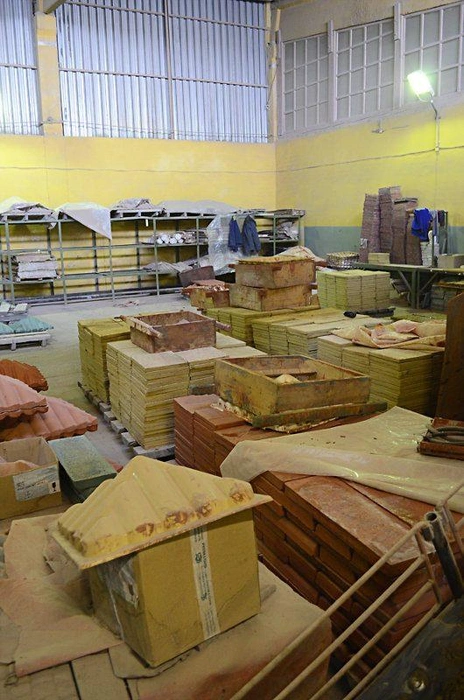
В эту ёмкость подаются цемент и песчано-гравийная смесь. Вручную, после завешивания на весах подаются красители и отвердитель, который делает поверхность глянцевой.
Затем масса перемешивается и вручную загружается в пластиковые формы. Залитые формы некоторое время стоят на вибростоле — чтобы раствор проник во все выемки — не оставляя пузырьков воздуха и выступающих камешков.
Готовые кирпичи уже не серые, а белые. На площадке около цеха их формируют в пакеты, а затем мостовым краном грузят в вагоны или грузовики. Вагоны разъезжаются по краю, а автомобили с логотипами «Энергожилстроя», «Регионального управления строительства» и других фирм — по Чите.